Local Exhaust Ventilation (LEV) Testing
Why is the LEV required?
Many substances used within the workplace can cause harm to health.
These substances could be dusts, vapours, gases, fibres or fumes. Ill health caused by these substances is preventable. The law requires companies to adequately control exposures to materials in the workplace that cause ill health. These are laid out in The Control of Substances Hazardous to Health (COSHH) Regulations.
Within the workplace we refer to the person who has the legal responsibilities or obligations regarding compliance with COSHH as the Duty Holder (DH).
“Every employer shall ensure that the exposure of his employees to substances hazardous to health is either prevented or, where this is not reasonably practicable, adequately controlled”. COSHH Regulation 7
Local Exhaust Ventilation is the primary control used to control substances hazardous to health.
What is LEV?
Local Exhaust Ventilation is an engineering system that has been designed, installed and commissioned to adequately control exposure, to the substances hazardous to health.
LEV effectively takes the dust, mists, gases, vapour or fumes out of the air to make sure they can be breathed in by the user, and others who may be exposed incidentally.
Note:
An LEV System rarely controls 100% of the substances hazardous to health. Consequently, it is important to understand the other control measures that would be used in conjunction with LEV as part of a wider control strategy eg training or respiratory protective equipment (RPE).
What are the main components of an LEV System?
Operator and Process & Hazardous substance: It is vital that the person undertaking the risk assessment and provides information on the prevention and control measures is competent to do so. Failing to correctly identify those at risk, the process or hazardous substances under control correctly can have disastrous consequences.
Hood: This is where the contaminant cloud enters the LEV examples include capture hoods, canopy hoods over a hot process or spray booths.
Airflow Indicator: This enables the operator to check if the system is operating as required.
Ducting: This moves the contaminated air from the hood to the exhaust discharge point.
Inspection Hatch: The design should incorporate the need for operator access for routine inspection and cleaning typically via an inspection hatch.
Test Points: The design needs to allow for safe access for routine testing.
Filter: This filters or cleans the contaminated air. Not all systems require these.
Fan: The ‘engine’ that provides the power to move the contaminated air. It draws air and contaminant from the hood, through ductwork, to discharge.
Discharge: Whether or not it has been cleaned, extracted air must not re-enter the building or enter other buildings unless the contaminant has reached negligible concentrations.
What is a Thorough Examination and Test (TExT)?
The aim of the LEV test is to enable the Duty Holder (DH) to fulfil their requirements as per Regulation 9 of the Control of Substances Hazardous to Health Regulations 2002 (as amended):
Our LEV Thorough Examination and Testing is undertaken using our four-part process called LEV Control Review:
Stage 1: Desk Top Study
Stage 2: Visual Inspection
Stage 3: Technical Measurements
Stage 4: Report
The objective is to ensure that every element of each LEV control measure performs as originally intended and continues to adequately control the exposures of employees to the substances hazardous to health.
Based on visual inspections and technical measurements, the tester will make a judgement as to whether the system is adequately controlling the substance(s) hazardous to health and provide a report which includes a decision on the effectiveness of each system.
How often does an LEV system need testing?
The maximum time between tests of LEV systems is set down in COSHH and for most systems this is 14 months.
Our testers would typically recommend a re-test in 12 months giving you a 2-month window of opportunity to get the testing undertaken again.
More frequent testing may also be recommended if it is anticipated that the system effectiveness will degrade between tests.
COSHH schedule 4 lists the intervals for TExT for certain processes such as grinding and polishing metal in a room for more than 12 hours per week or casting process.
The test report needs keeping for at least five years.
Competency
Our team includes BOHS Certified Competent, LEV Testing Specialists, listed in the Professional Standards Authority Accredited Register. They also include Specialist Licentiate Members of the British Occupational Hygiene Society (BOHS).
We typically work with clients involved with large construction projects in the Nuclear and Ship Building Sectors, Universities, Hospitals and Pharmaceutical.
Proven Process: LEV Control Review
This is an impartial audit of your overall COSHH Control Strategy (inc. Risk Assessment, LEV Specification, LEV Design, LEV Installation & Thorough Examination & Testing).
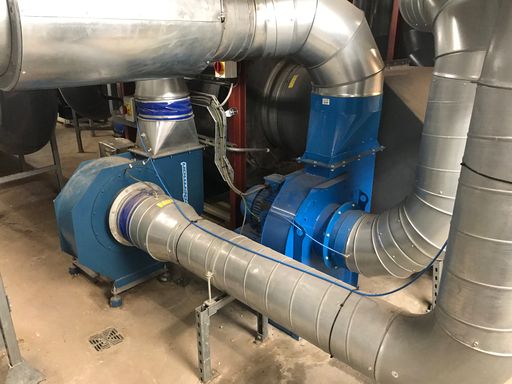
Request a Consultation
Get in touch
The first stage is to, either give us a call on 0191 378 2164 or fill out the contact us form and we’ll get back in touch to discuss your requirements.
We will then arrange a visit to your site, or if we have sufficient information, we’ll put a clear proposal together for you, with no hidden costs.
All being well our competent consultants will then visit site to undertake the work and produce a comprehensive report, reviewing your control measures with concise recommendations.
We operate throughout the UK and Worldwide.